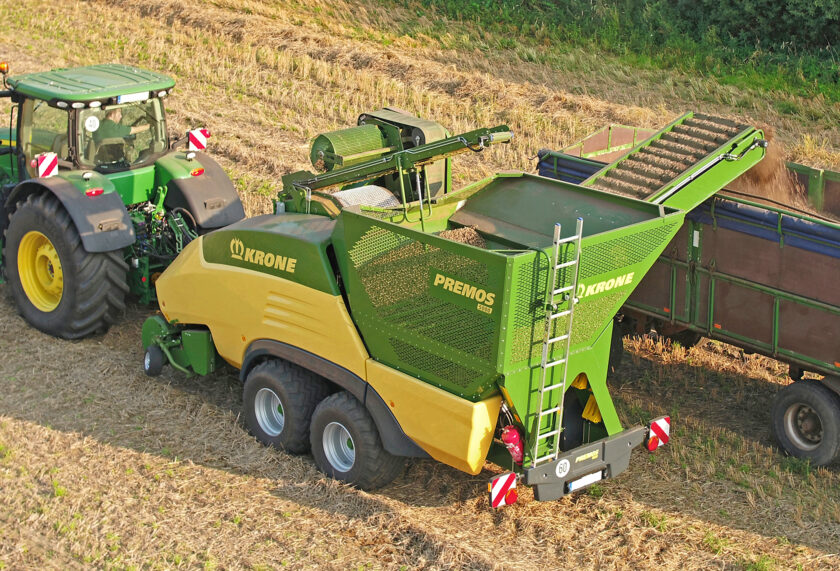
The first European Directive in favor of animal welfare dates back to 18 November 1974 and concerned the obligation to stun animals before slaughter. Today this may seem trivial, but 50 years ago the animal was not yet considered a sentient being and was therefore treated as a mere object. Since then, various other European initiatives have followed, such as the Amsterdam Protocol on the protection and welfare of animals in 1999. Especially in recent years, laws have come into force on the minimum spaces to be ensured for farmed animals, as are also Strict rules have been established on hygiene and comfort to be ensured for livestock. Furthermore, specific European contributions are linked to compliance with these rules and if the breeder does not treat his animals well, no contributions.
Among the virtuous practices in this sense is the care of litter boxes. These must have a high absorbent power, also lending themselves to being easily distributed and then removed once their task has been completed. Furthermore, they must not produce dust, since through this some diseases can spread more easily in farms.
Pellets are strategic
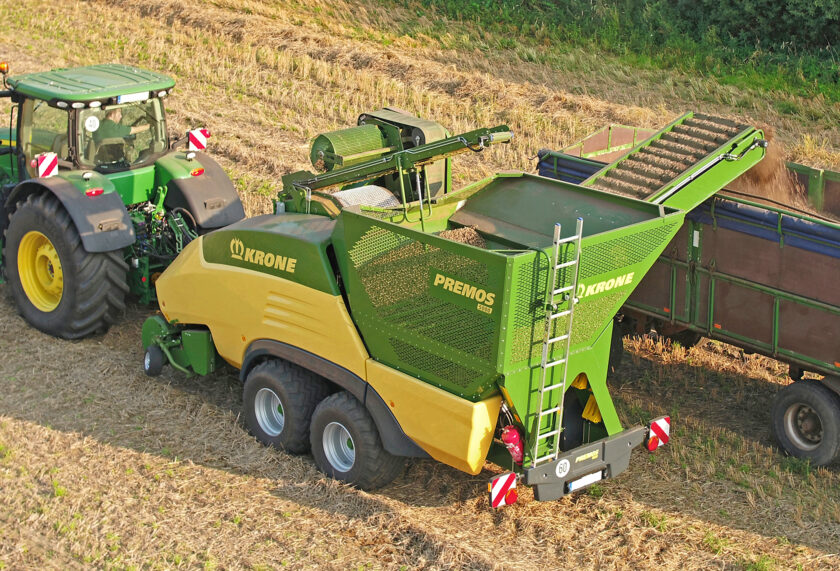
Last but not least, used litter must be able to be used as soil improvers or to fuel biogas production plants. In this sense, cereal straw pellets are well suited, which in addition to satisfying the above requirements can even be used as fuels in heating systems with reduced environmental impact. The problem is that it can become very expensive to collect large volumes of straw, transport it and finally pelletize it on the farm. Columbus’s egg is therefore the possibility of pelleting the straw directly in the field, shredding it and then compressing it in order to minimize the volumes to be handled and at the same time ensuring the delivery of a ready-to-use product to the company.
Real self-propelled work sites
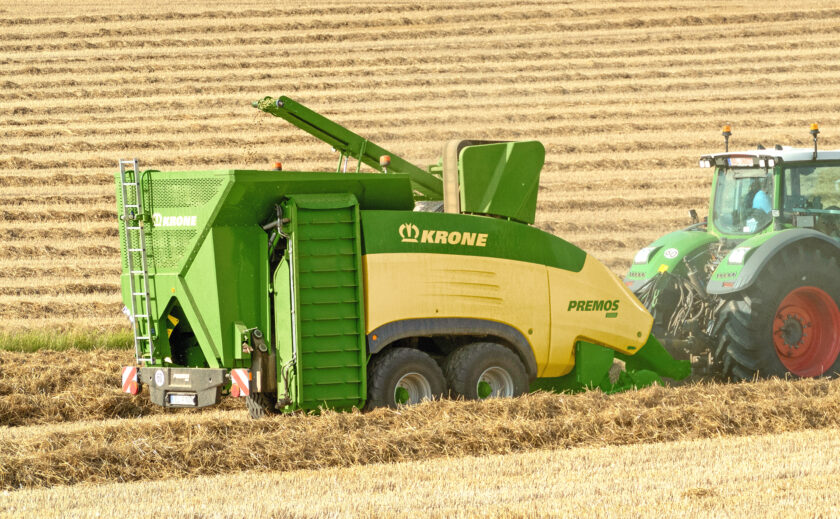
The “Premos 5000” pelletizers are aimed at this mission profile, the only ones on the market at the moment, which rather than machines in themselves should be considered real work sites in the field. In fact, they can collect and then shred the straw swaths as a large square baler would do, only to then press the harvest in a hot-humid environment to create robust cylindrical pellets. Transferred to a storage tank, the pellets can then be transferred to a transport wagon for sending to the company.
Up to five tons per hour
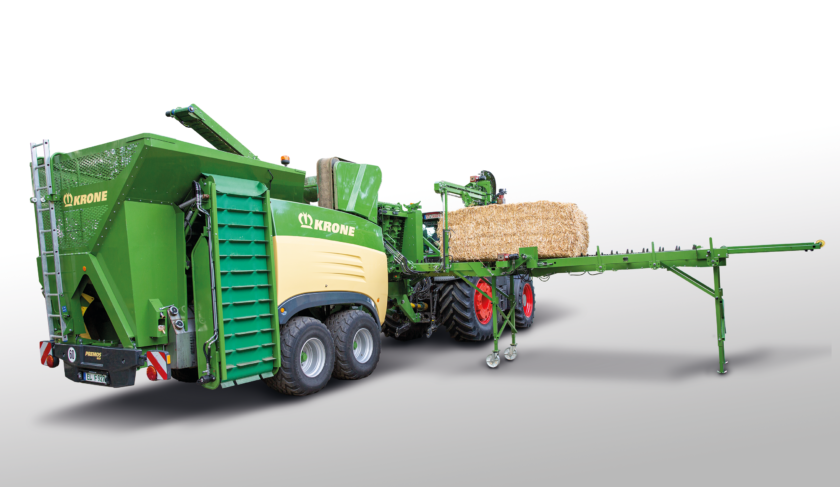
The machine initially operates thanks to a 235 centimeter wide pick-up which allows it to collect swaths of straw at a rate of five tons per hour, equivalent to a surface area of between 12,500 and 14,000 square meters considering straw production between 35 and 40 quintals per hectare. From the pick-up the straw is then conveyed to a cutting rotor which chops it up to the size necessary for pelleting.
The pieces are then taken by an auger which deposits them on a conveyor belt responsible for feeding the compression and extrusion system, made up of two rollers equipped with alternating teeth and holes. The chopped straw enters the holes, is compressed by the teeth and then extruded in the form of cylindrical pellets with a diameter of 16 millimetres.
The structural solidity of the pellets is achieved through a balanced combination of pressure and heat, with the former reaching two thousand bars and the latter, due precisely to compression, reaching 80 degrees centigrade. This process also allows the finished product to be sanitized, maintaining a residual humidity between 12 and 15 percent, i.e. the optimal level to guarantee the necessary cohesion of the material.
Optional smart humidification
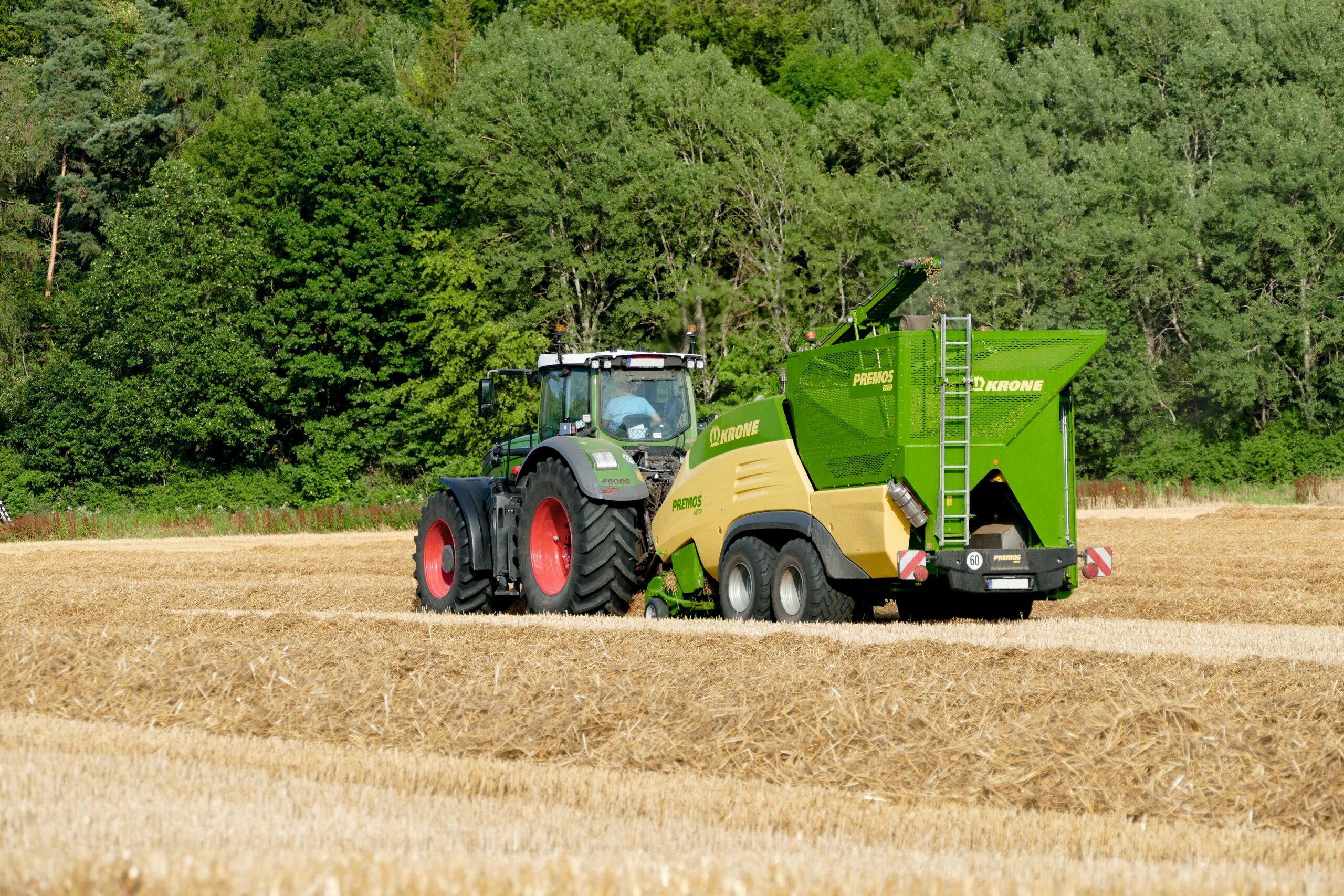
To this end, the “Premos 5000” can also be equipped with an intelligent humidification system, supplied as an option to those who work on particularly dry products. Once extruded, the pellets will then be transferred to the machine tank by a second integrated system of augers and conveyor belt. Finally, when the container is full, the transfer of the pellets to the transport wagons will be delegated to a third belt, all to guarantee maximum respect for the structure of the pellets themselves.
Small volumes but high density
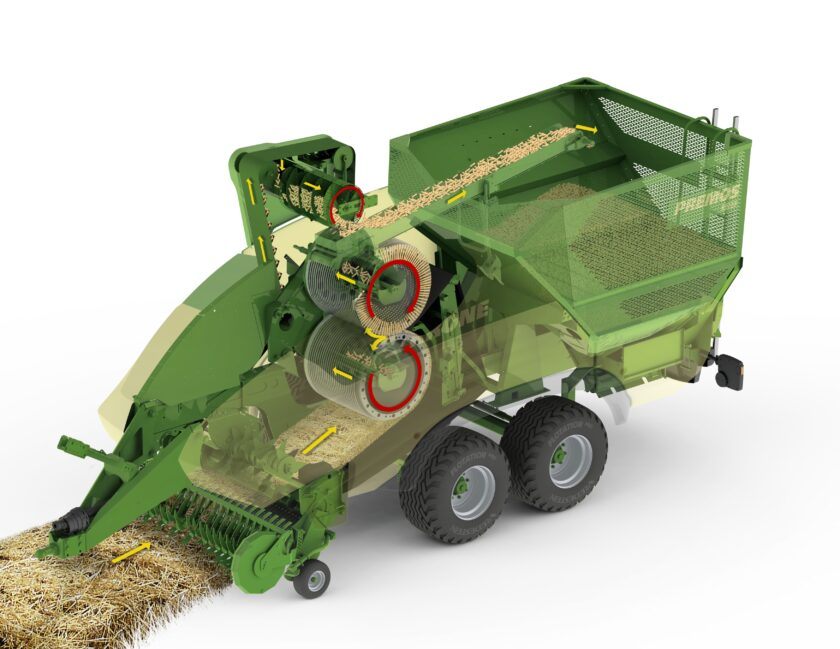
Thanks to the pelleting process, the volume to be transported will be three to four times lower than that represented by the straw as such, thus positively impacting the energy and management balances of the entire process. Furthermore, the high density of the pressed material will offer significant absorption capacity. One kilo of pellets can in fact absorb up to four liters of water, swelling progressively to the point of decay. A point that obviously must be anticipated by removing the material from the litter and sending it to subsequent treatments aimed at reusing it for other purposes, i.e. added to manure or inserted into biodigesters.
The performance as a fuel is also interesting, given that two and a half kilos of pellets are equivalent to approximately one kilo of heating oil of fossil origin. It should also be noted that from this year a lateral feeding system is available which allows the “Premos 5000” to be used statically and therefore as fixed company equipment. This extends the seasonal periods of use, favoring a more rapid amortization of investments. From this perspective it is worth specifying that according to Krone the Krone “Premos 5000” can give rise to productions of just under five quintals of finished pellets per hour, a product which if inserted into a digester gives rise to an energy return equal to that proposed by over 11 quintals of corn silage.
Titolo: Krone “5000” pelleting machines, more unique than rare
Autore: Redazione